Achieve the optimum axle-guide linkage profile
Introducing HALL® Hydraulic Elastomers
Good curving behaviour and stable high-speed running in axle guide bearings have traditionally been seen as mutually exclusive characteristics – if you achieve one, you compromise on the other. Now, however, there’s no longer any need to compromise, thanks to HALL® hydraulic axle guide bearings.
The ideal combination of minimum cost and maximum performance
- Frequency-dependent performance delivers low stiffness in curves and greater stiffness at high speeds
- Reduced friction conserves energy and cuts your lifecycle costs
- Easy fitting and exchange ability with conventional bearings keep your track access charges to an absolute minimum
- Immediate usability – there’s no need to modify your vehicles
- Reduction of wear on wheels and rails
- Greater protection of vehicles and platforms
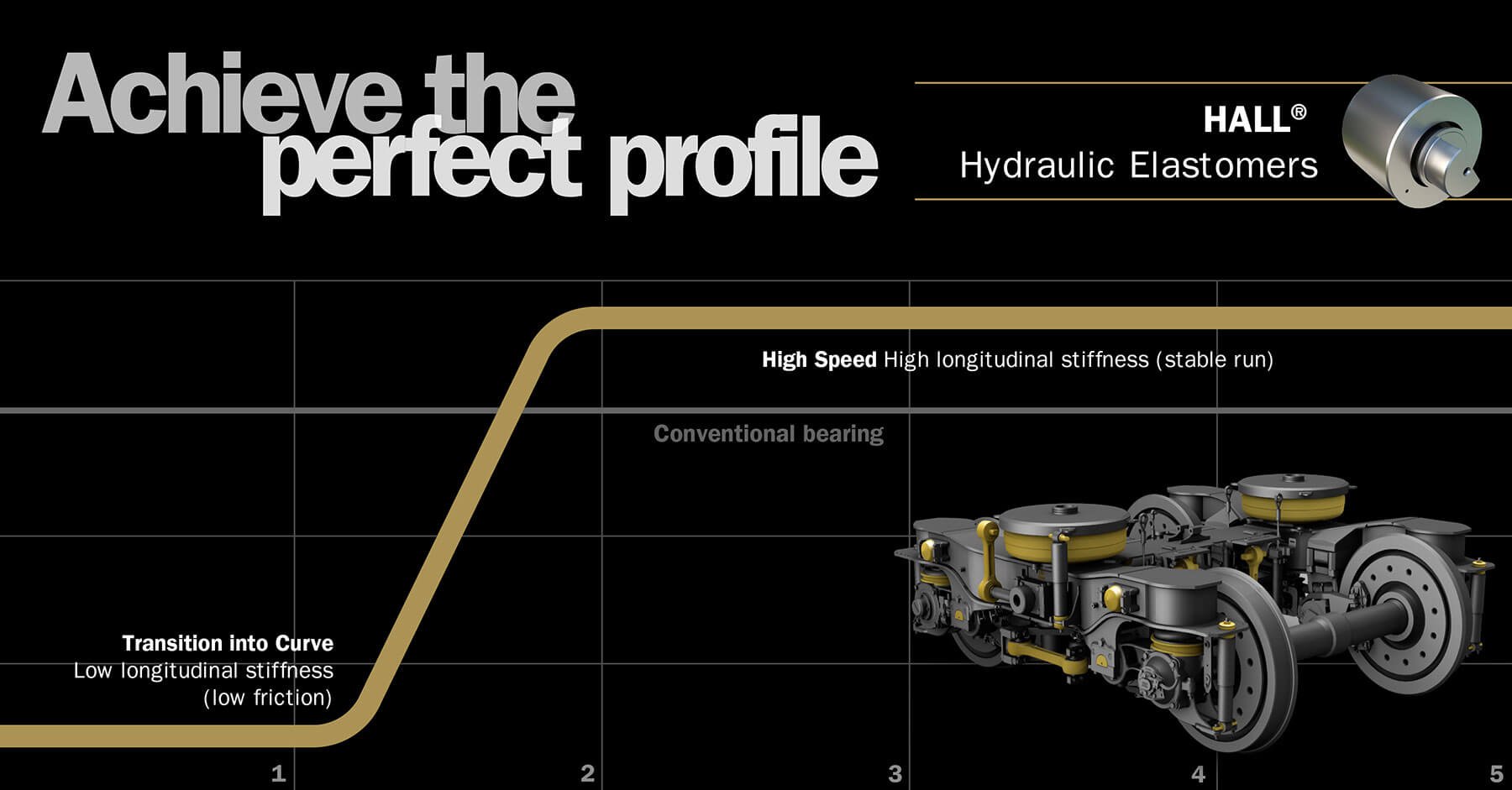
HALL® – Hydraulic axle guide bearings
With HALL®, you can combine the low longitudinal stiffness for curves with the high longitudinal stiffness for movement in a straight line in a single component. The hydraulics integrated hydraulics lead to frequency dependent changes of the longitudinal stiffness.
The hydraulic axle guide bearing can be designed in such a way that a low stiffness is automatically available during steady adjusting movements when entering or exiting a curve. The bearing stiffness increases during dynamic excitation at higher speeds. As the HALL® fits in the existing space for conventional axle guide bearing, it can be integrated in new, as well as existing, vehicles without structural modifications to the bogie.
What could you save with HALL®?
Try our online calculator to discover how much you could save by adding HALL® to your rail vehicles. Once you’ve tried the online version, get in touch with us for an even more detailed picture of your savings, taking into account:
- The number of years between changing parts
- Class of train
- Fuel type
- Wear on bearings
- Reprofiling wheels
These initial results are based on simulations using a fixed and varied route (varied meaning some turns and some straights), using an approved 185hb/m train.
To calculate your savings, simply select the appropriate information below.
Engineered to perform
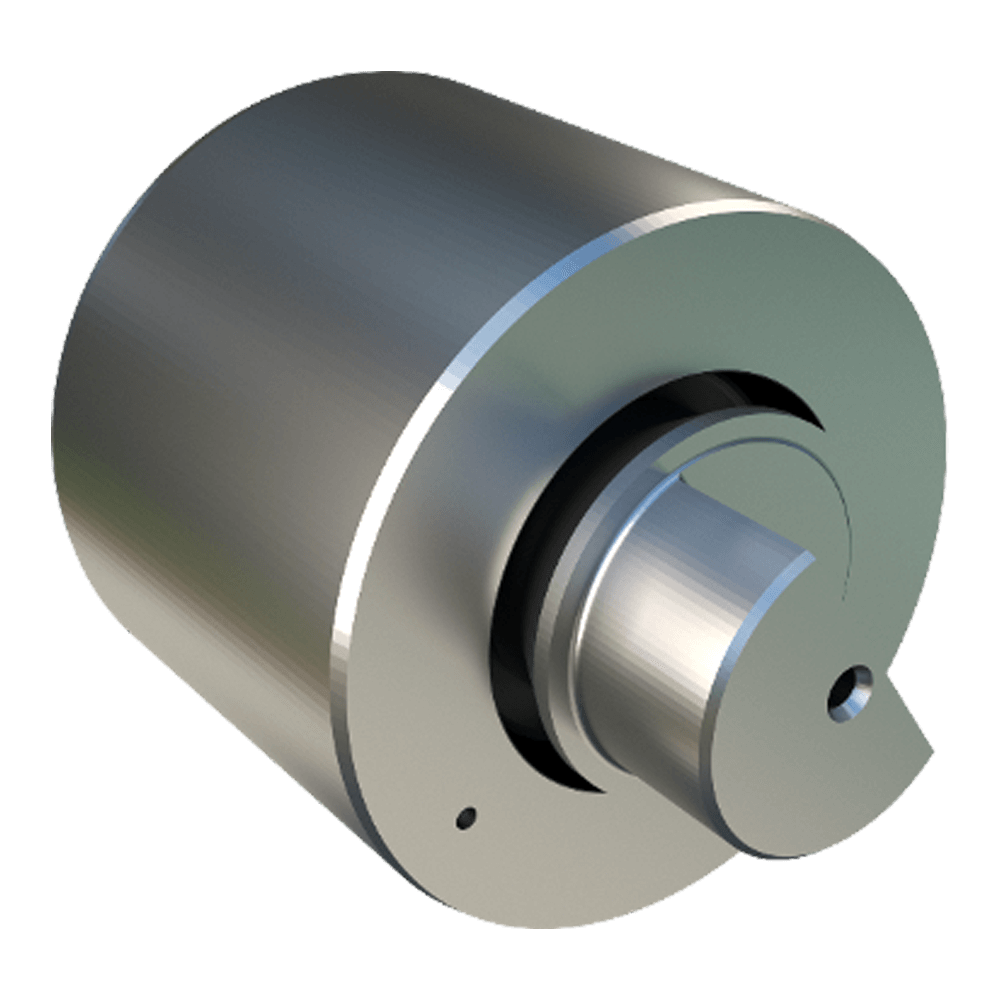
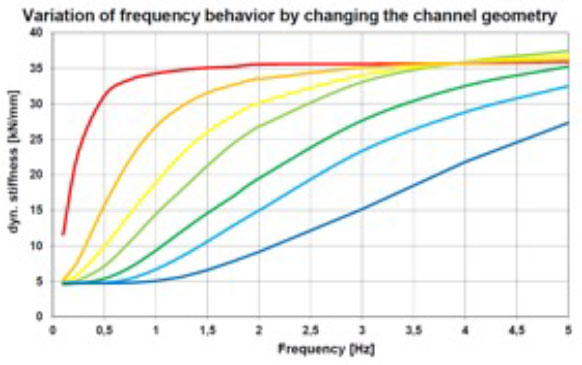
(project specific)
(project specific)
(project specific)
Reducing wear, cutting costs
Infrastructure maintenance costs represent a significant part of the overall cost of railway operations. Increasing axle loads, higher speeds and the greater axle control stiffness required have seen this cost spiral further in recent years.
Recent intensive studies in the UK and Sweden on the relationship between vehicle properties and the wear of wheel and rail were conducted, leading to new fee models for the track access. These models reward flexible axle control with lower fees.
Measurements in the vehicles secured with HALL® show a significant regression of wear and rolling contact fatigue (RCF) in wheels and rails.
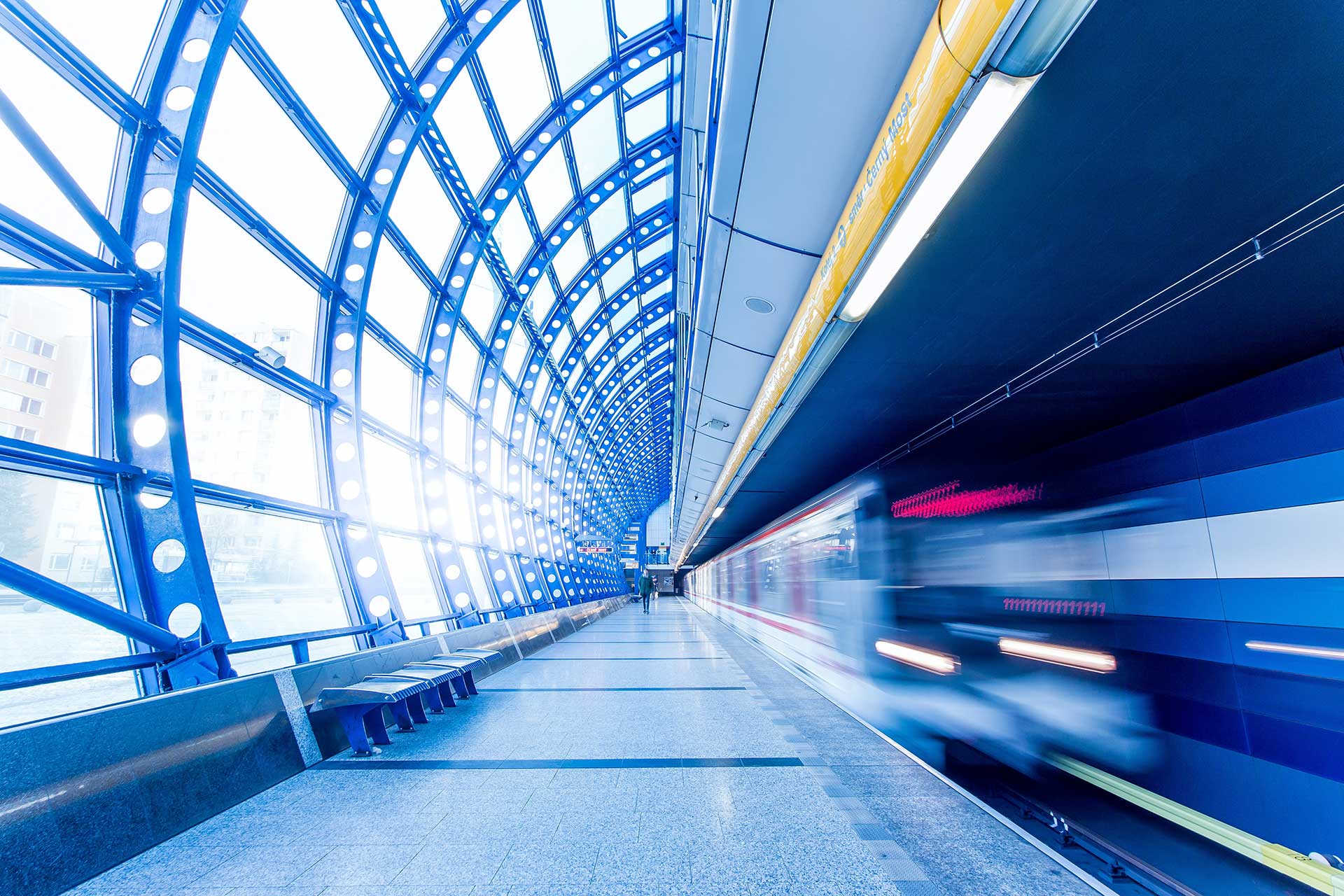
1.1 million miles without losing performance
In a recent customer test, HALL® hydraulic axle guide bearings were shown to continue delivering the optimum combination of outstanding curving behavior and stable high-speed running, even after 1.1 million miles.
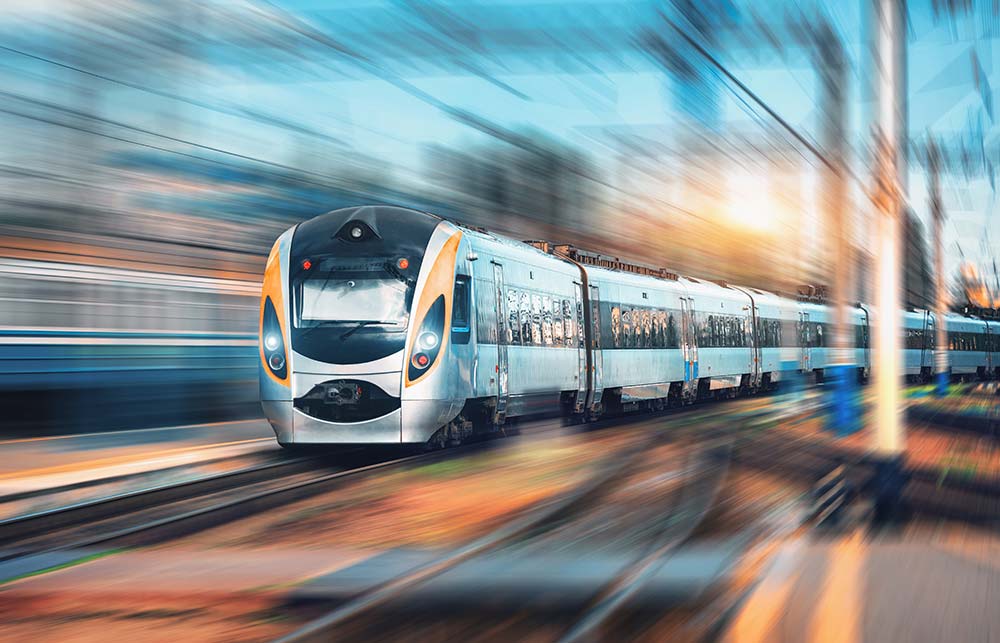
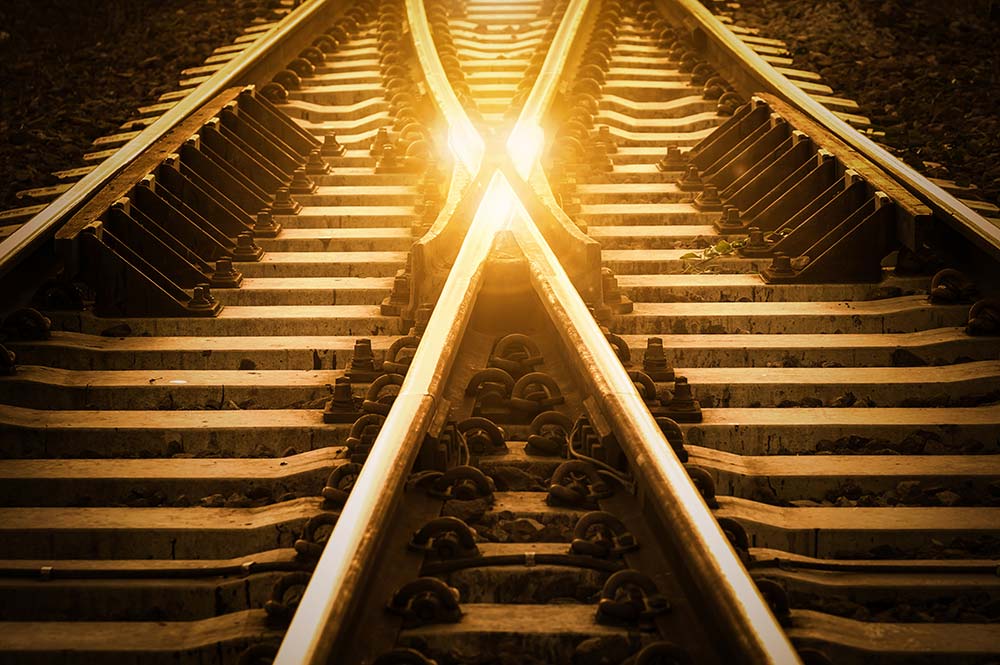
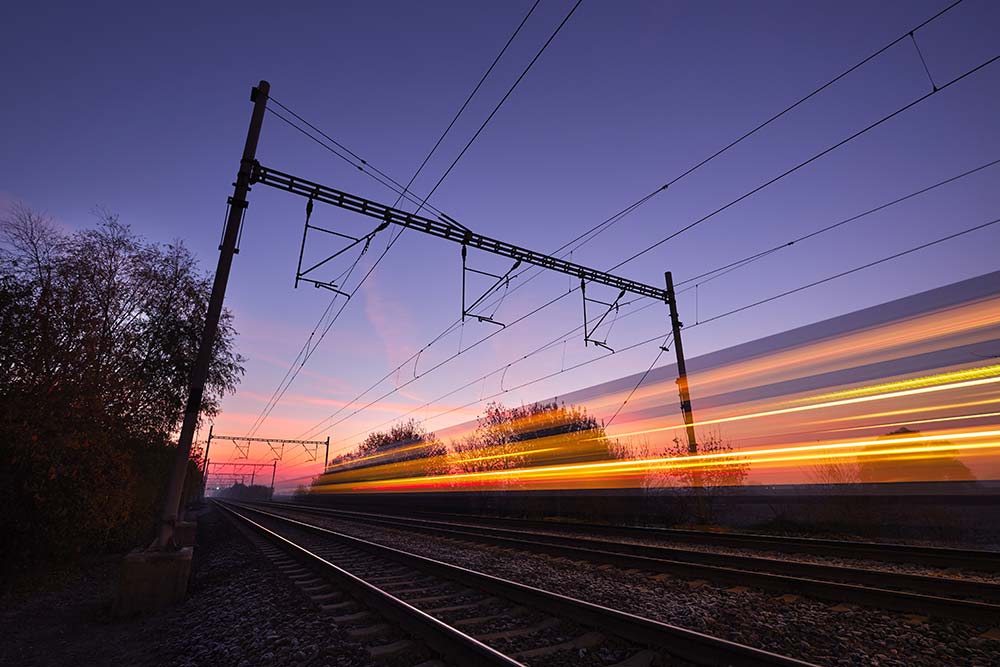
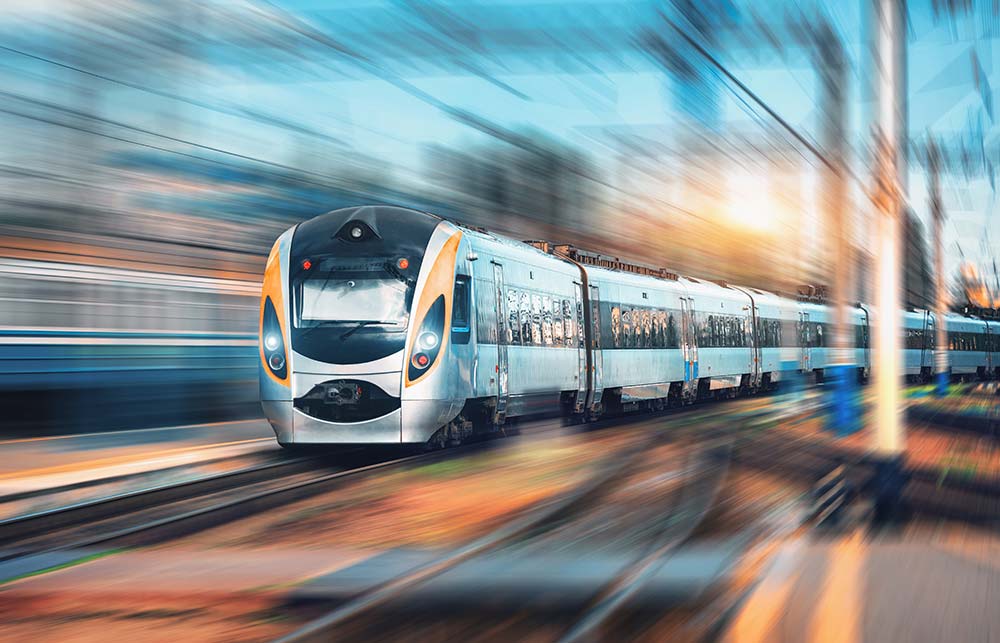
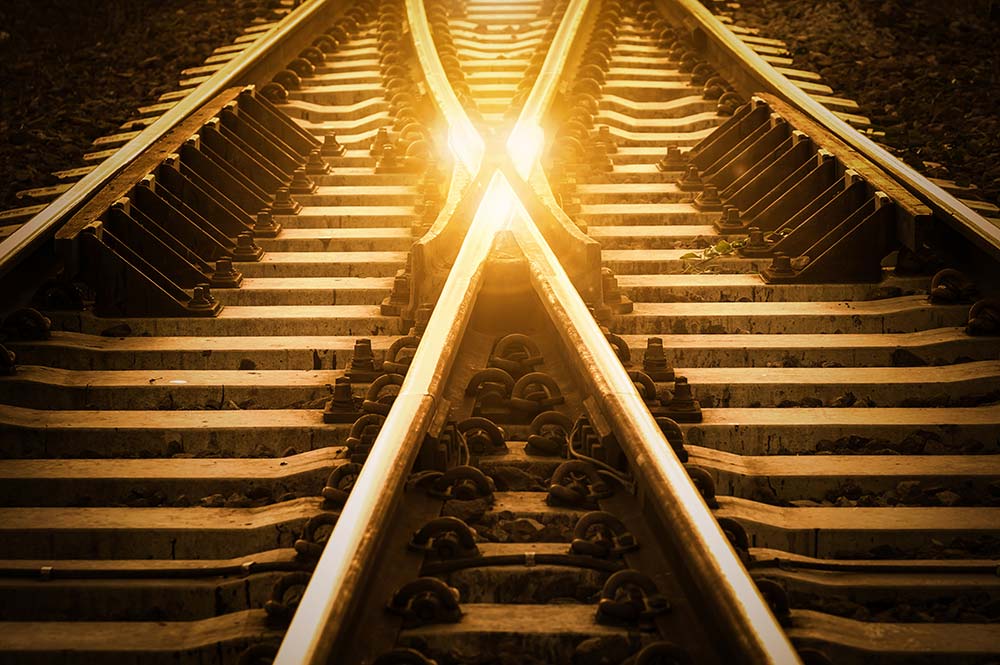
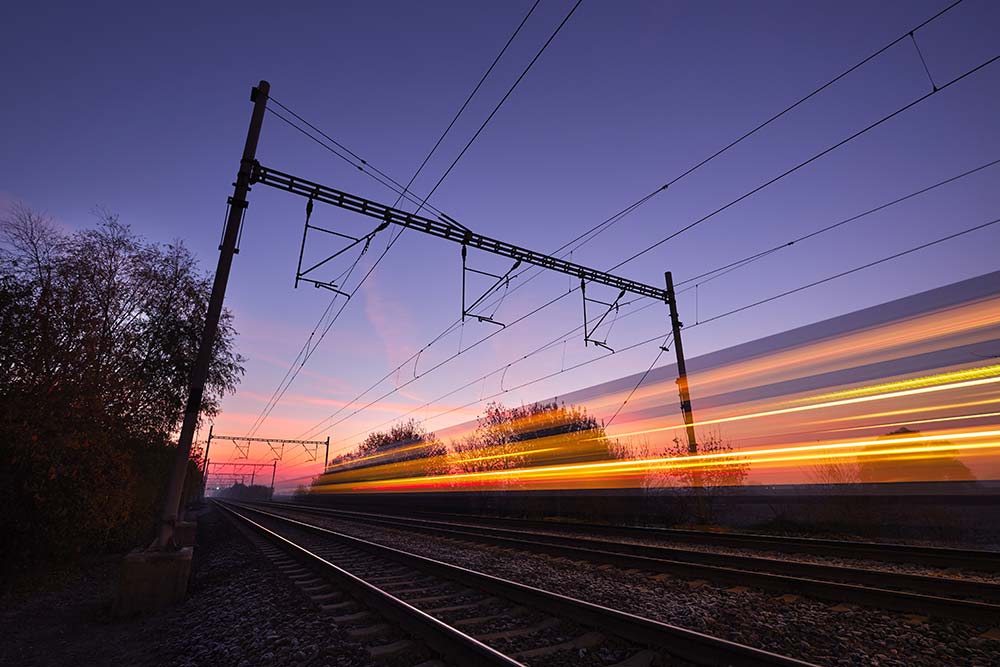